Thickness gauges
Thickness gauges play a big role in this mission by providing accurate, reliable measurements essential for quality control, process optimization, and compliance with industry standards. In this comprehensive guide, we dive into the world of thickness gauges—covering the fundamentals, the differences between contact, laser, and X-ray technologies, detailed comparisons, and practical guidance to help you choose the right solution for your application.
What are thickness gauges and why are they critical in manufacturing?
At its core, a thickness gauge is an instrument designed to measure the thickness of materials with high precision. Whether used on metal sheets, plastic films, or coatings, these devices ensure that manufacturing processes remain within tight tolerances and meet quality assurance benchmarks. For engineers, plant managers, and quality control professionals, a reliable thickness gauge not only validates product integrity but also minimizes waste, reduces rework, and optimizes production efficiency.
Key benefits include:
Key benefits include: Thickness measurements confirm that products adhere to design specifications.
Quality assurance: Regular monitoring helps maintain compliance with ISO standards and industry regulations.
Process optimization: Real-time data from inline systems supports continuous improvement in manufacturing.
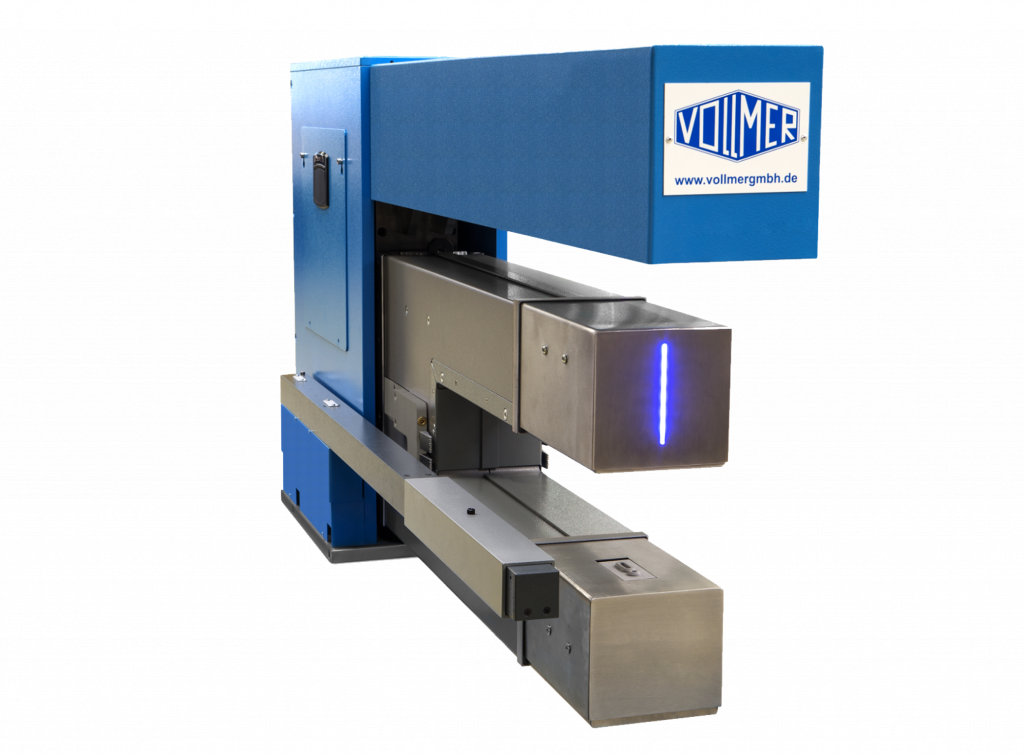
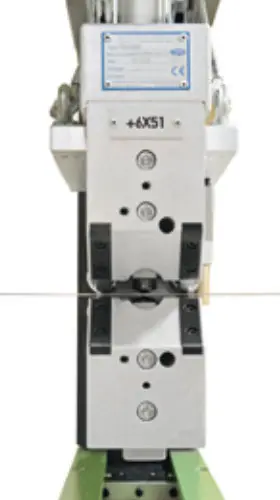
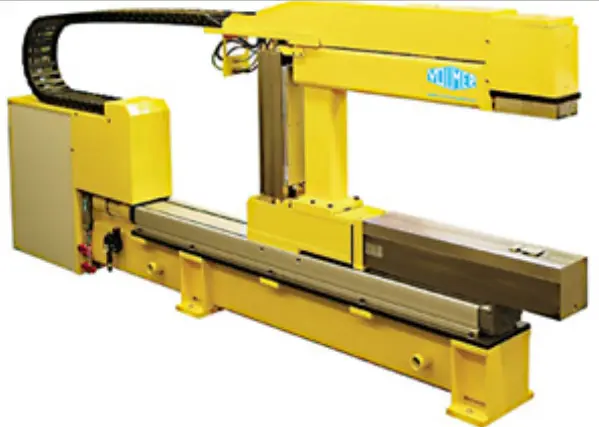
Overview: Different Types of Thickness Gauges
Modern measurement technology offers various solutions tailored to different industrial challenges. The primary types of thickness gauges include:
Contact Thickness Gauges: Använder taktila mätmetoder med direkt fysisk kontakt.
Laser Thickness Gauges: Employ non-contact, optical methods to measure thickness at high speed.
Each type offers distinct advantages depending on the material, production environment, and specific measurement needs.
Contact Thickness Gauges – Proven precision through tactile measurement
How do contact gauges work?
Contact thickness gauges operate by physically touching the material with two sensors—one on the top surface and one on the bottom. The sensors, often equipped with diamond-tipped transducers, measure the distance between the surfaces, providing highly accurate results even at micrometer levels. The process typically includes an automatic zeroing feature, ensuring that measurements remain precise over time.
Applications
Strip Production: Vanligt förekommande i valsverk och glödgaller där metallens tjocklek övervakas kontinuerligt.
Quality Inspection: Essential in service centers and calibration labs where absolute accuracy is needed.
Metrology Labs: Serve as reference instruments due to their proven precision and reliability.
Technical Specifications
Mätområde: Vanligtvis 0,01–24 mm.
Noggrannhet: Mikrometer-nivå, ofta ±1 µm.
Speciella funktioner: Sensorvinkelkompensation för att hantera vågiga material samt automatisk nollställning vid coilbyte.
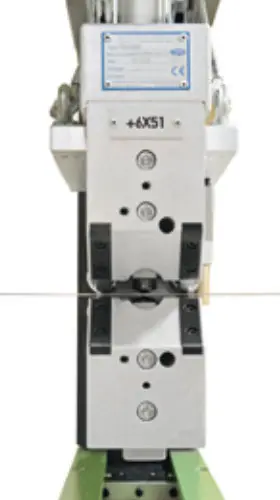
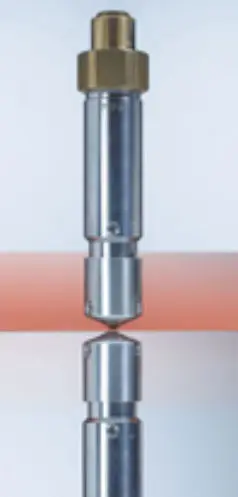
Laser Thickness Gauges – Non-contact accuracy at 50 kHz speed
How do laser gauges work?
Laser thickness gauges, such as the advanced VTLG system, utilize a non-contact optical method. The system employs a rigid C-frame equipped with two synchronized laser sensors that measure the distance from the strip surface to each sensor. With a scanning rate of up to 50 kHz, these systems capture high-speed data, enabling real-time process control even in dynamic environments.
Applications
Inline Production Control: Ideal for cold rolling and high-speed production lines where real-time monitoring is essential.
Automated Inspection: Supports full automation with rapid data processing and integration into control systems.
Dynamic Environments: Robust against temperature variations and airborne contaminants, thanks to integrated air cleaning and temperature compensation.
Technical Specifications
Scanningshastighet: Upp till 50 kHz, vilket möjliggör nästan omedelbara mätningar.
Noggrannhet: ±1 µm under optimala förhållanden.
Självkalibrering: Använder interna referensblock (captive gauge blocks) för automatisk kalibrering under drift.
Miljötålighet: Funktioner som automatisk luftfiltrering och temperaturkompensation säkerställer hög precision även under tuffa förhållanden.
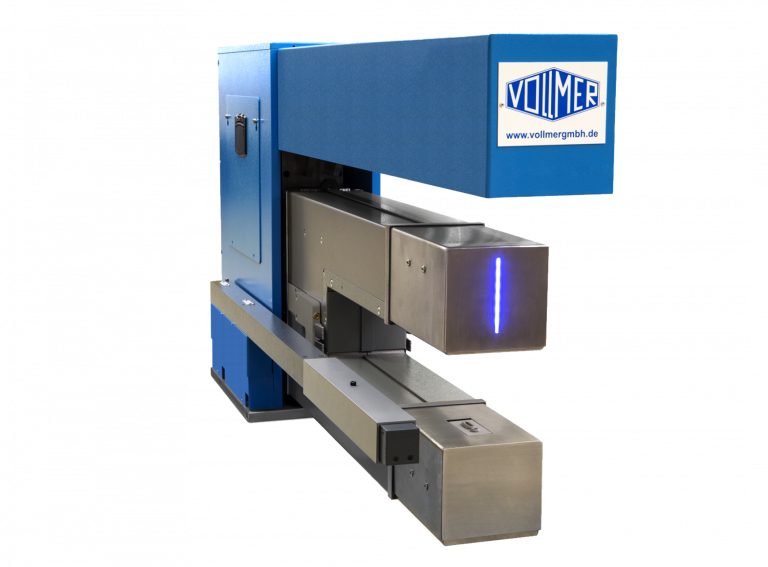
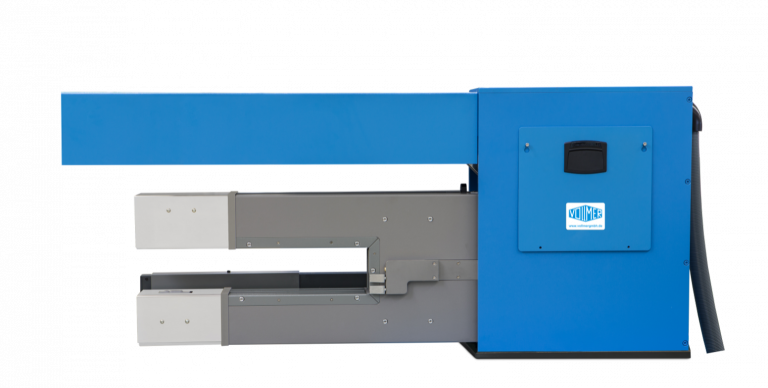
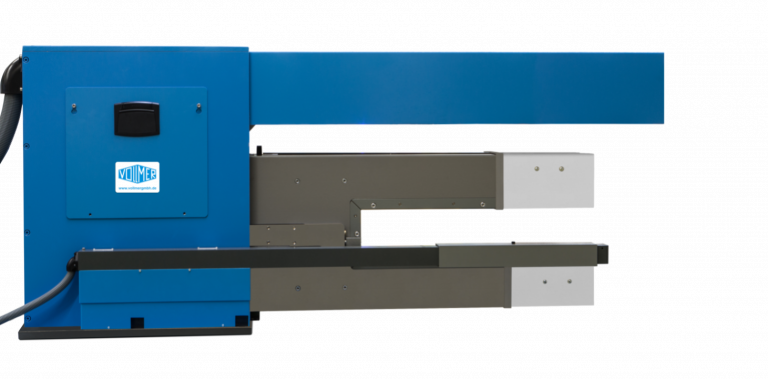
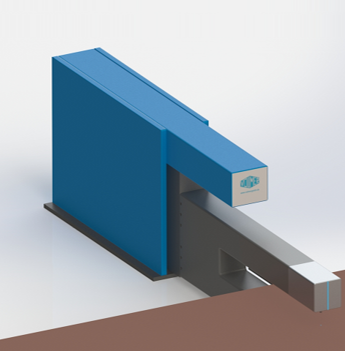
X-Ray Thickness Gauges – Reliable non-contact solutions for complex materials
How do X-ray gauges work?
X-ray thickness gauges use radiometric technology to measure material thickness without physical contact. These systems can be either X-ray or isotope-based, using digital detectors that minimize signal noise. X-ray gauges are especially useful for measuring multi-layered or coated materials where other technologies might struggle to deliver consistent results.
Applications
Coated Materials: Perfect for applications requiring the measurement of thin films or multiple layers.
Complex Composites: Ideal for non-destructive evaluation of composite materials where traditional methods fail.
High-Speed Environments: Compact and non-invasive, they are well-suited for inline inspection on fast-moving production lines.
Technical Specifications
Kompakt design: Vissa system har en C-ram så smal som 120 mm, vilket passar i trånga utrymmen.
Digitala detektorer: Ger lågt signalbrus och hög precision.
Alloykompensation: Alternativ med kalibreringsplattor eller kemisk analys säkerställer noggrannhet oavsett materialvariation.
Underhållsvänlighet: Innovativa lösningar, som en utbytbar tungstenlåda, förenklar rutinunderhåll och säkerhetsrutiner.
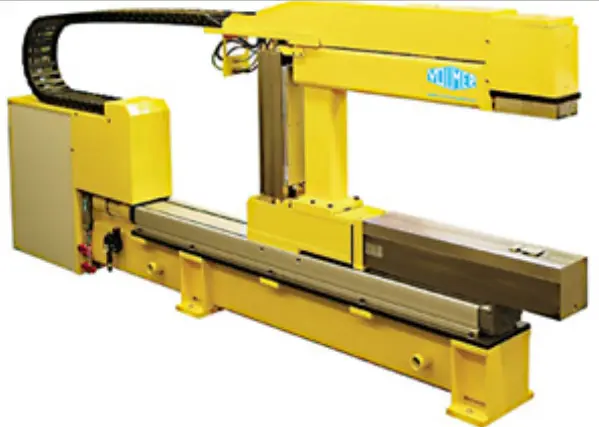
How to Choose the Right Thickness Gauge for Your Application
Selecting the appropriate thickness gauge involves considering several factors that directly impact your production quality and process efficiency. Use the following checklist to guide your decision:
Material Type:
Are you measuring metals, plastics, or composite materials?
Do you require alloy-independent measurement?
Strip Width and Thickness:
What is the range of material thickness you need to measure (e.g., 0.01–24 mm)?
Production Environment:
Is your production line operating at high speeds requiring real-time data?
Are environmental factors such as temperature variations and airborne particulates a concern?
Automation Level:
Do you need a gauge that integrates seamlessly into automated systems (e.g., PLC-controlled environments)?
Maintenance and Calibration:
How critical is minimal downtime for calibration and maintenance?
Would automatic calibration and self-check features add value to your process?
Budget Considerations:
Do you require the most cost-effective solution, or are you willing to invest in a higher-end system with advanced features?
Answering these questions will help you determine whether a contact, laser, or X-ray gauge best meets your specific application requirements.
Contact Us
Contact us today for expert advice, a personalized quote, or a product demonstration. Let our experience and technical expertise guide you to the measurement solution that will elevate your quality assurance processes and drive operational excellence.